As India’s electric vehicle (EV) drive picks up speed, is local content staying in step? While some of the leading companies are doing design and development of most parts of the vehicle inhouse – including the battery pack, powertrain, electrical & electronic system, motor, controller, digital dashboard, the frame and suspension – localisation of manufacturing of parts and components is still at low levels, though rising. This localisation is important because it could help to lower EV prices, and make vehicle repair less expensive. EV industry experts say the current local content, particularly in critical parts, would not be much more than 15-20%, and that localisation could reduce the prices of these parts by up to 30%.
While some of these critical parts are beginning to get locally produced, their scale and availability are still 18-24 months away. Sohinder Gill, director general of the Society of Manufacturers of Electric Vehicles, the apex body for EVs in India, says the primary challenge is in manufacturing the drivetrain, specifically motor, battery and battery management systems (BMS) within the country.
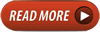